- Home
- Blog
- Powerful 1500mmx3000mm Fiber Laser Cutting Machine with options of 500w, 700w, and 1000w Laser Sources: Efficient and Precise Cutting Technology
Powerful 1500mmx3000mm Fiber Laser Cutting Machine with options of 500w, 700w, and 1000w Laser Sources: Efficient and Precise Cutting Technology
By:Admin
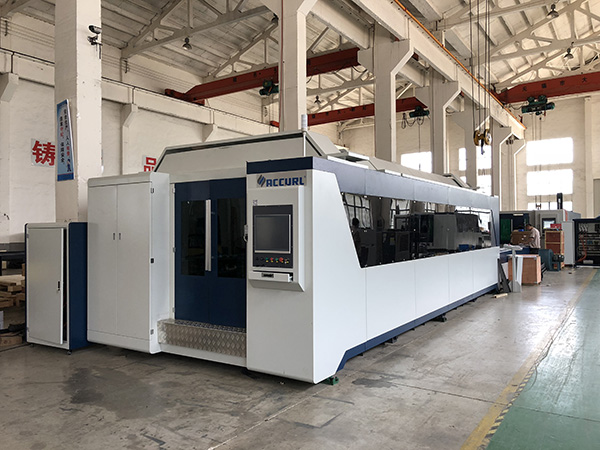
Cutting metal, plastics, wood, and other materials often used in construction, manufacturing, and industrial applications is a challenge without a laser cutting machine. Though many types of laser cutting machines are available, the Co2 Laser Cutting Machine 500w stands out for its unparalleled efficiency, reliability, and quality.
A Co2 Laser Cutting Machine is a highly efficient, yet affordable cutting tool that uses a mixture of gases and a focused beam of laser energy to cut through metals and other tough materials. The 500w laser source is perfect for small businesses and startups looking to cut materials with precision and high-quality results.
Compared to traditional cutting methods, Co2 Laser Cutting Machines are faster, more accurate, and require lower maintenance. The fiber transmission used in this cutting machine guarantees a consistent quality cutting effect in every point of the material being cut. The technology has been specially designed to reduce gas consumption and increase photoelectric conversion efficiency, which can reach up to 35%.
The 1530 fiber cutting machine 500w is a high-performance machine that can cut through a wide range of materials, including steel, stainless steel, aluminum, brass, copper, and other non-metal materials such as acrylic and plastics. The machine's accuracy is excellent, and the use of fiber transmission ensures a consistent and reliable cutting result.
The Co2 Laser Cutting Machine 500w is also an excellent tool for precise cutting of intricate geometric patterns. The machine's cutting speed is fast, and the exactitude is exceptional at every point. Plus, the machine's software can be programmed to cut almost any shape or design that you need, or you can simply upload your design, and it will automatically start cutting.
With the ability to cut materials of varying thicknesses, Co2 Laser Cutting Machines are versatile and can be used for various projects in different industries. Additionally, the cutting machine has excellent cutting capacity and high processing quality. And, because of these characteristics, the machines are ideal for particular industries, including building and construction, automotive, and other manufacturing industries requiring high precision cuttings.
In summary, the Co2 Laser Cutting Machine 500w is an excellent choice for cutting through a wide range of materials with high precision and accuracy. The machine not only saves time but also minimizes material wastage and guarantees high-quality results. Whether you are in the manufacturing, automotive, or construction industry, this machine can help you achieve your goals and realize the full potential of your business.
Company News & Blog
Key Maintenance Tips for Industrial CNC Routers in Woodworking
Investing in an industrial grade CNC router machine is a significant decision for any woodworking business. To ensure the longevity, performance, and dependability of the machine, it is crucial to maintain it correctly and efficiently. Daily, weekly, monthly, and quarterly maintenance measures help protect your CNC router and ensure maximum uptime. In this blog post, we will cover daily maintenance procedures that woodworkers can carry out to keep their router machines in excellent working condition.Daily Maintenance:Daily maintenance measures are quick and easy, often taking less than ten minutes. The following are some of the daily tasks that woodworkers can perform to ensure the optimal performance of their CNC router machines:1. Clean the machine: Use a soft and dry cloth to wipe down the machine's exterior and remove any dust, debris, or dirt that may accumulate on the surface. This not only keeps the machine looking clean and maintained, but it also prevents the debris from entering the internal components.2. Check the coolant level: Ensure that the coolant is at the right level for the machine's spindle and refill it if needed. Low coolant levels may cause the machine to overheat, resulting in damage to the spindle or other integral components.3. Check the air filter: Check the air filter if the router machine has one and make sure it is clean. A dirty air filter can reduce airflow to the machine's spindle or motor, causing it to overheat or malfunction.4. Check the lubrication system: Check the machine's lubrication system to ensure that it is working correctly. Make sure there is enough lubrication for the spindle and other moving parts. Running the machine without adequate lubrication can cause premature wear and tear, leading to additional maintenance costs in the long run.5. Inspect the tooling: Inspect the tooling before use. Ensure that the cutters, bits, and other tools are sharp and in good condition. Dull or damaged tools can cause the machine to work harder and produce a low-quality output.In conclusion, by carrying out these daily maintenance procedures, woodworkers can keep their CNC router machines in excellent working order and avoid unwanted downtime. It is essential to invest time and effort in maintaining the machine and follow the manufacturer's guidelines to ensure the machine's optimal performance and longevity.
3-in-1 Welding Cart: The Ultimate Solution for All Your Welding Tools
Innovation is the key to success, especially when it comes to finding new ways to tackle difficult tasks. This is true in every industry, including agriculture. Farmers have to deal with a wide range of challenges that can be difficult to overcome. One of the most significant challenges in farming is maintenance. Farmers use a variety of tools to maintain and repair their equipment, and these tools need to be easily accessible and portable. This is where the 3-in-1 welding cart comes in.The 3-in-1 welding cart is a portable, all-in-one solution for farmers who need to have their welding equipment and supplies on hand. The cart is designed to hold a MIG welder, a TIG welder, and a plasma torch, as well as a welding helmet and other supplies. The cart is made from a three-drawer tool box that has been modified with angle iron. The angle iron has been added between the wheels and a box that extends 12 inches to create a shelf on top of the angle iron that can hold two tanks.The elevated shelf is where farmers can set their plasma torch, which is an essential tool for cutting and welding metal. The plasma torch is designed to create a high-temperature plasma arc that can be used to cut through thick metal quickly and efficiently. The plasma torch is a complex tool that requires specialized equipment and supplies. The elevated shelf on the 3-in-1 welding cart is the perfect place to store these supplies, such as replacement tips, electrodes, and other consumables.One of the best things about the 3-in-1 welding cart is that it is portable. Farmers can easily move the cart from one location to another without having to disassemble it or worry about it taking up too much space. The cart is designed to be lightweight and easy to maneuver, even on rough terrain. This makes it an ideal solution for farmers who need to work in remote or difficult-to-reach locations.In conclusion, the 3-in-1 welding cart is a revolutionary tool that is perfectly suited for the needs of farmers. With its ability to hold a wide range of equipment and supplies, it is an essential piece of equipment for anyone who needs to maintain or repair their equipment on the farm. The portability and ease of use make it an ideal solution for farmers who need to work in challenging conditions. If you're a farmer looking for a way to streamline your maintenance and repair processes, the 3-in-1 welding cart is definitely worth considering.
Mastering CNC 3D Machine Carving: Tips on Choosing the Best Bits
CNC 3D Machine Carving: Bringing Your Woodworking to LifeWoodworking has been a popular hobby for centuries, but technology has taken it to a whole new level in recent years. The development of CNC (computer numerical control) machines has revolutionized the woodworking industry, allowing for precision cuts and intricate designs to be made with minimal effort. One of the most exciting things you can do with a CNC router is 3D carving, bringing your woodworking projects to life like never before.But what exactly is 3D carving? Simply put, it's the process of using a CNC machine to carve intricate three-dimensional designs into wood. Instead of simply cutting a flat surface, a 3D carving can add depth and texture to your projects, making them truly stand out. However, choosing the right bits for the job is crucial to achieving the desired results.When it comes to 3D carving, the most commonly used bits are ball nose and bull nose bits. Ball nose bits are great for carving curved surfaces and contours, while bull nose bits are better suited for flat bottoms and sharp edges. Other popular bits include tapered bits, which are great for carving tight spaces and deep grooves, and V-bits, which can create sharp corners and angles.It's important to note that different materials will require different bits. For example, harder woods like oak or maple will require larger, stronger bits than softer woods like pine or cedar. It's also important to consider the depth and complexity of your design when selecting bits. A shallower design may require a smaller bit, while a more intricate design may need a larger bit to properly capture all the details.Once you've selected the right bits for your project, it's time to start carving. The key to successful 3D carving is patience and precision. Take your time and make sure your machine is properly calibrated to avoid any mistakes or errors. It's always a good idea to test your design on a scrap piece of wood before committing to your final project.In conclusion, 3D carving on a CNC machine is a fantastic way to take your woodworking projects to the next level. With the right bits and some patience, you can create stunning, intricate designs that will have everyone asking, How did you do that? So why not give it a try? Who knows what amazing designs you'll come up with on your 3D woodworking machine.
Efficient and Smooth Laser Cutting Services for Steel Tubes
Laser Cutting Technology at Steel CompaniesThe world of steel production has undergone a number of transformations thanks to technological advancements. One of the most significant transformations is the shift from traditional cutting methods to laser cutting. Steel companies that have adopted this technology have experienced a plethora of benefits, including increased accuracy, faster production rates, and greater flexibility in design. In this article, we will discuss how laser cutting works and its advantages over traditional cutting methods.Laser Cutting OverviewLaser cutting is a process that involves the use of a high-powered laser beam to cut materials such as steel, aluminum, and other metals. The laser beam is directed by a computer program that controls the direction, intensity, and duration of the beam to produce a precise cut. The laser beam heats the material to the point that it vaporizes, creating a clean and efficient cut.Laser cutting can be performed on a wide range of materials, including flat sheets, tubes, and other structural components. In addition to steel and aluminum, laser cutting can also be used on brass, copper, titanium, and other metals.Advantages of Laser CuttingPrecisionLaser cutting is extremely precise and accurate, capable of producing cuts to within 0.1mm. This level of precision is essential in industries such as aerospace and automotive, where the slightest deviation can have serious consequences. Laser cutting is also ideal for intricate designs that require intricate cuts.SpeedLaser cutting machines can operate at a much faster pace than traditional cutting methods. This means that steel companies can produce parts and components much faster than they could using traditional cutting methods. The speed of laser cutting also means that less time is spent on set-up and maintenance, further reducing production times.FlexibilityLaser cutting is incredibly versatile and can be used to cut a wide range of shapes and sizes, even those with complex contours. This means that steel companies can produce designs that were once impossible or impractical using traditional cutting methods.Energy EfficientLaser cutting is an energy-efficient technology, with minimal waste produced during the cutting process. The laser beam itself is also incredibly energy efficient, consuming less power than traditional cutting methods.SafetyOne of the key advantages of laser cutting is its safety. Unlike traditional cutting methods that require blades, saws, and other cutting tools, laser cutting does not produce any physical contact between the cutting tool and the material. This means that there is less chance of injury or accidents occurring during the cutting process.Barrett Steel and Laser CuttingAs one of the largest steel companies in the UK, Barrett Steel has embraced laser cutting technology in its operations. The company's tubes division operates state-of-the-art laser cutting systems that are capable of handling a wide range of materials and specifications.The laser cutting machines used by Barrett Steel tubes division are incredibly precise, producing accurate cuts to within 0.1mm. The machines are also incredibly versatile, capable of producing intricate designs and shapes that were once impossible using traditional cutting methods.Barrett Steel's laser cutting technology has resulted in significant benefits for both the company and its customers. The accuracy and speed of the laser cutting machines have led to faster production times and greater flexibility in design. The machines are also energy-efficient, producing minimal waste and consuming less power than traditional cutting methods.ConclusionLaser cutting technology has transformed the world of steel production, providing companies with greater precision, speed, and flexibility in design. Steel companies that have adopted laser cutting technology, like Barrett Steel, have experienced numerous benefits, making the technology an essential part of their operations. As technology continues to advance, it is certain that laser cutting will continue to be an important tool in the world of steel production.
Metal Sheet Cleaning Made Easy with Fiber Laser Technology
Metal Sheet With Fiber Laser Cleaner - Benefice of Bransgore and Hinton AdmiralThe world is changing and industries are fast adopting modern technologies to improve their efficiency and productivity. The metal sheet cleaning industry is no exception. In fact, the industry has been one of the early adopters of fiber laser cleaning technology. Fiber laser cleaning has revolutionized the metal sheet cleaning industry, and Bransgore and Hinton Admiral are now beneficiaries of this technology.Fiber lasers are highly efficient and reliable sources of laser beams. The cavity converts the low-quality diode light into single-mode laser light. One of the fiber Bragg gratings acts as a total reflector, while the other serves as a partial reflector or output coupler. The solid-state architecture of fiber lasers makes them insusceptible to environmental factors such as dust, moisture, and free-space air perturbations.The technology is not only efficient but also eco-friendly. It replaces traditional cleaning methods that use chemicals, which are not only harmful to the environment but also have the potential to cause long-term harm to humans. Fiber laser cleaning completely eliminates the need for chemicals and produces no toxic waste that could find its way into the environment.Lockdown across the globe has, undoubtedly, had a negative impact on the economy. Many businesses have had to shut down or work at limited capacity, and the metal sheet cleaning industry has not been spared. However, some businesses have managed to find ways to thrive, and one such company is Bransgore and Hinton Admiral. They have been able to leverage the benefits of fiber laser cleaning to offer their clients a safe and affordable cleaning service.Unlike traditional cleaning methods, fiber laser cleaning does not damage the substrate material. The laser beam selectively removes contaminants on the surface of the metal sheet while leaving the substrate material intact. This has been a major selling point for Bransgore and Hinton Admiral, as damage to the substrate material could result in additional costs for their clients.The cleaning system offered by Bransgore and Hinton Admiral is fast, efficient, and reliable. The system uses state-of-the-art scanners that are capable of removing contaminants quickly and accurately. The system allows their clients to clean large surface areas in a short amount of time thus improving their productivity. This has been particularly helpful for clients who have had to work under limited capacity during the lockdown.The technology is not only efficient but also safe for the operators. Fiber laser cleaning does not produce harmful fumes that could put the operators at risk. The system is also easy to operate, and Bransgore and Hinton Admiral have invested in the training of their operators to ensure that they can offer their clients a seamless service.The fiber laser cleaning technology has been a game-changer in the metal sheet cleaning industry. It has not only improved the efficiency and productivity of businesses but also has had a positive impact on the environment. Bransgore and Hinton Admiral have been able to leverage the technology to offer their clients a safe and affordable cleaning service. The lockdown may have had a negative impact on the economy, but businesses like Bransgore and Hinton Admiral have shown that it is possible to thrive in difficult times with the right technology and mindset.In conclusion, the technology offers numerous benefits to the metal sheet cleaning industry. It is fast, efficient, and reliable, and has a positive impact on the environment. With more businesses adopting the technology, the industry can look forward to a more productive and eco-friendly future.
Discover the Benefits of CNC Milling in Melbourne's School of Design
CNC Milling - The Future of ManufacturingIn the current digital age, CNC milling has established itself as one of the most important technological advancements in the field of manufacturing. CNC milling or Computer Numerical Control milling is the process of using computer software to control precision cutting and shaping machinery. It has revolutionized the process of manufacturing and has paved the way for more accurate and efficient production techniques. In this blog post, we will delve deeper into the world of CNC milling, its benefits, and its applications in the Melbourne School of Design CNC milling industry.The Melbourne School of Design (MSD) CNC milling program is a prime example of how CNC milling can enhance the learning process in design schools and workshops. Through CNC milling, the students at MSD learn how to create accurate and functional prototypes using a range of mediums. They are able to transform their designs from computer models to real-life objects with ease and in turn, gain valuable knowledge in manufacturing and design.One of the biggest advantages of CNC milling is its precision. Through the use of computer software, the machinery is able to execute instructions with incredible accuracy, making it possible to create complex shapes and designs that were previously unachievable. Additionally, CNC milling machines have the capacity to operate 24/7, making them an ideal choice for large-scale production.Another major benefit of CNC milling is its cost-effectiveness. Since the process is automated, it requires very little manual labor, reducing labor costs. Furthermore, the software used to operate the machines is relatively cheap, making it cost-effective for both small and large-scale manufacturers.CNC milling has a wide range of applications in various industries. It’s used in the aerospace industry to create parts for airplanes and spacecrafts. In the automotive industry, it’s used to create prototypes and parts for automobiles. It's also commonly used in the jewelry industry to create intricate designs. The applications of CNC milling are endless, and it’s no wonder why it’s become an indispensable tool for manufacturers worldwide.Milling router is a critical component of CNC milling and is responsible for achieving the high level of accuracy that comes with this process. It's essentially a spinning cutting tool that’s used to remove material from a workpiece in a controlled and precise manner. The cutting tool is mounted onto the milling router and is moved along an X, Y and Z-axis to shape the workpiece.In conclusion, CNC milling is a game-changer in the manufacturing industry and has numerous advantages when compared to traditional manufacturing processes. The precision, cost-effectiveness, and wide range of applications make it a powerful tool that is redefining the way products are made. The Melbourne School of Design's CNC milling program is a perfect example of how this technology can be used to enhance design education and produce skilled professionals in the field. As CNC milling continues to evolve, we can expect to see even more applications and incredible developments in the field of manufacturing.
High-Precision Fiber Laser Cutting Machine for Efficient Metal Processing
CNC Fiber Laser Cutting Machine: The Innovation in Metal Cutting TechnologyOver the years, different advancements in technology have been made for different industries. One of the biggest beneficiaries of technological advancements is the manufacturing industry, and specifically the metal cutting industry. With the introduction of CNC Fiber Laser Cutting machines, manufacturers can cut different kinds of metal materials with a high precision and speed like never before.CNC Fiber Laser Cutting machines have gained immense popularity in the manufacturing industry. Companies like Shandong Pengwo Laser Technology Co., Ltd. have been at the forefront of designing and manufacturing CNC Fiber Laser Cutting machines that are efficient, precise, and reliable. The machine uses a fiber laser generator and ball screw moving system that enable it to cut and punch different types of metal materials without compromising on quality.Features of CNC Fiber Laser Cutting Machines1. High Cutting Precision:CNC Fiber Laser Cutting Machines have a high cutting precision that enables them to deliver top-notch end products. The laser is transmitted through a fiber, which ensures that there is no loss of energy, and hence precision cutting is achieved. Whether you need to cut intricate designs or thick metals, CNC Fiber Laser Cutting Machines will deliver.2. High Speeds:The use of advanced fiber laser technology with ball screw moving systems enables CNC Fiber Laser Cutting machines to achieve high speeds while cutting, without compromising the precision. By increasing the production speed, your manufacturing process will become more efficient, and your business will be more profitable.3. Low Maintenance:One of the biggest advantages of installing CNC Fiber Laser Cutting Machines is its low maintenance. Since the laser is transmitted through a fiber, there is no need to adjust or maintain the laser optical path. In contrast, traditional laser cutting machines require frequent maintenance, which can be costly and time-consuming.4. Energy Efficiency:CNC Fiber Laser Cutting Machines have excellent energy efficiency compared to other traditional metal cutting methods. The advanced fiber laser technology used in these machines significantly reduces the amount of energy consumed, which in turn helps to lower your operating costs. It is an environmentally friendly cutting option with no emissions of harmful substances.5. Versatile:CNC Fiber Laser Cutting Machines can cut different types of metals, including steel, stainless steel, aluminum, copper, and brass. This versatility makes them indispensable in the manufacturing process as they offer a wide variety of options to cut different shapes and sizes of metal materials.Conclusion:CNC Fiber Laser Cutting Machines are the latest innovation in the metal cutting industry. They offer a plethora of features that make them indispensable to the manufacturing process. High precision, high speed, low maintenance, energy efficiency, and versatility are some of the unique selling points of CNC Fiber Laser Cutting Machines. By incorporating them into your manufacturing process, you will increase efficiency, profitability, and precision cutting. So, if you are looking for an efficient and reliable way to cut metals, CNC Fiber Laser Cutting Machines are definitely worth considering.
Sale Begins for New Type of CNC Milling Machine: 3D Cutting Technology
Possible article:New Desktop CNC Milling Machine Enables Precision Prototyping and Small-Scale ProductionSan Francisco-based company has released a new version of its desktop CNC milling machine, which allows users to create complex designs from a wide variety of materials. The Othermill Pro improves on the original Othermill model, adding faster spindle speeds, larger working volume, and more advanced software features. With its compact size and user-friendly interface, the Othermill Pro is suitable for both professional makers and hobbyists who want to turn their ideas into physical objects with high accuracy and detail.The Othermill Pro is a type of subtractive manufacturing technology, which means that it removes material from a block or sheet of material through cutting, drilling, and engraving. This differs from additive manufacturing, such as 3D printing, which builds up layers of material to form a shape. While 3D printing has become popular for prototyping and customization, CNC milling machines are preferred for producing precise parts, molds, and fixtures that require tight tolerances, smooth surfaces, and dimensional stability.The Othermill Pro can work with a range of materials, including aluminum, brass, copper, Delrin, FR-1/4, polycarbonate, acrylic, and various types of wood and circuit board substrates. It uses a 1/8 end mill to carve out geometries from 2D or 3D CAD files, which can be imported from common design software such as Autodesk Fusion 360, Eagle PCB, and KiCAD. The spindle of the machine can rotate at speeds up to 10,000 RPM, allowing for fast and efficient machining of parts.One key feature of the Othermill Pro is its automatic tool calibration system, which enables the machine to adjust the height and position of the cutting tool based on the thickness and flatness of the material. This ensures that the milling process is accurate and consistent, even when working with irregular or non-uniform surfaces. The machine also has a built-in dust collection system, which collects debris and prevents the workspace from getting messy or hazardous.The Othermill Pro comes with a software package that is designed to be user-friendly and intuitive, even for those with little or no experience in CNC milling. The software allows users to import their designs, select the material type and thickness, set the cutting parameters, preview the toolpath, and simulate the machining process. The software also includes features such as engraving, pocketing, drilling, and chamfering, as well as the ability to create PCB traces and pads for electronics projects.According to the company, the Othermill Pro is ideal for prototyping, research and development, small-batch manufacturing, and even educational purposes. It can be used to make precision mechanical parts, artistic sculptures, custom jewelry, signage, molds for casting, and electronic circuits. The machine is also compatible with a range of fixtures and clamps, which allow for secure and efficient material handling. With its quiet operation, compact footprint, and stylish design, the Othermill Pro can fit into any workspace or home lab.The Othermill Pro is available for purchase on the website and through authorized resellers. The machine comes with a one-year warranty and free technical support, as well as a starter kit that includes cutting tools, materials, and accessories. The company also offers online tutorials, forums, and user community resources to help users get the most out of their machine. With the release of the Othermill Pro, aims to empower makers and inventors to turn their ideas into reality, one precision cut at a time.
Polyurethane Belt Welding Machine for Seamless Connectors - 220V, Temperature Range of 180-200 Degrees, Achieves Perfect Belt Forming
BAOSHISHAN PU Round Belt Welding Machine: The New Revolution in Polyurethane Belt Hot Melt TechnologyBAOSHISHAN, a leading technology company that specializes in the development of advanced welding machines, has recently released a new product on the market - the PU Round Belt Welding Machine. This machine is designed to weld polyurethane round belts using a hot melt process, thus providing a much stronger and more efficient connection between the belts.The machine is made from the highest quality materials and is available in several different models, each with its own unique features and capabilities. Regardless of which model you choose, you can be sure that your welding projects will be completed quickly and efficiently, with minimal downtime and high-quality results.One of the most significant advantages of the BAOSHISHAN PU Round Belt Welding Machine is its temperature range. The welding machine usually ranges from 180 to 200 degrees Celsius, which is perfect for welding polyurethane belts without damaging them. This ensures that your belts will remain strong and durable, even after years of continuous use.Another feature that sets the PU Round Belt Welding Machine apart from its competitors is its belt forming effect. With this machine, you can easily form belts into a perfect circle, which gives them a cleaner and more professional look. Plus, this feature guarantees a much tighter connection between the belts, ensuring that they stay in place even under heavy loads.The machine is also very versatile, making it suitable for use in a wide range of industries, including automotive, packaging, construction, and many more. Whether you need to weld belts for conveyor systems, packaging machines, or industrial equipment, the BAOSHISHAN PU Round Belt Welding Machine can handle it all.Furthermore, the machine is incredibly easy to use, thanks to its simple design and intuitive controls. Even if you're not familiar with welding machines, you'll be able to operate this machine with ease, thanks to its user-friendly interface and detailed instructions.In conclusion, the BAOSHISHAN PU Round Belt Welding Machine is an excellent choice for anyone looking to improve the quality and durability of their polyurethane belts. With its advanced features, high-quality materials, and ease of use, this machine is sure to exceed your expectations and provide you with the best possible results. So why wait? Order your BAOSHISHAN PU Round Belt Welding Machine today and experience the new revolution in polyurethane belt hot melt technology!
CNC Cutting Machine Manufacturers and Suppliers in China - Seek Cooperation for Mutual Benefits
The world of manufacturing is constantly evolving to keep up with the demands of customers. One innovation that has revolutionized the manufacturing industry is Computer Numerical Control (CNC) machines. These machines use computer-aided software to operate and control the movements of precision cutting tools that cut through various materials, including steel. CNC steel cutting machines have become increasingly popular in industrial settings due to their precision, speed, and efficiency.At Qianyi Steel CNC Cutting Machine Manufacturers in China, we are committed to producing high-quality and reliable CNC steel cutting machines that meet the needs of our customers. Our machines are designed to offer maximum performance, accuracy, and speed, making them ideal for a wide range of industrial applications.One of the primary benefits of CNC steel cutting machines is their ability to produce consistently precise cuts. The computer-controlled machines are programmed to follow specific cutting patterns, and the cutting tools are designed to cut through materials with extreme accuracy. This precision is particularly critical in manufacturing, where even small deviations in cutting can lead to significant production issues.Another significant advantage of CNC steel cutting machines is speed. These machines can cut through steel much faster than manual cutting methods, making them an ideal option for large-scale industrial operations. Additionally, CNC machines can operate for extended periods without the need for frequent maintenance, ensuring consistent performance and reliability.At Qianyi Steel CNC Cutting Machine Manufacturers, we believe in delivering customized solutions to meet your specific requirements. We offer a wide range of CNC steel cutting machines, including plasma cutters, laser cutters, waterjet cutters, and flame cutters, ensuring that you can find the machine that best meets your needs.In conclusion, CNC steel cutting machines offer manufacturing companies a range of benefits, including precision, speed, and efficiency. As a leading manufacturer of these machines, Qianyi Steel CNC Cutting Machine Manufacturers is committed to providing our customers with high-quality equipment that meets their specific needs. Contact us today to learn more about our products and services and see how we can help improve your manufacturing operations.